Divertissement
10 Astuces pour Optimiser l’Efficacité de la Gestion des Matériaux dans Votre Entrepôt
Optimiser l’efficacité de la manutention est essentiel pour maximiser la productivité des entrepôts. En fournissant aux employés le bon équipement de manutention, comme des racks et des chariots, on améliore non seulement l’organisation, mais aussi la rapidité des opérations. Une planification judicieuse de l’agencement de l’entrepôt, associée à une formation continue du personnel, crée un environnement de travail sûr et efficace. En intégrant des systèmes automatisés et en optimisant les horaires d’arrivée des camions, les entrepôts peuvent réduire les temps d’attente et améliorer le flux de marchandises. Investir dans ces stratégies est la clé d’une rentabilité accrue.
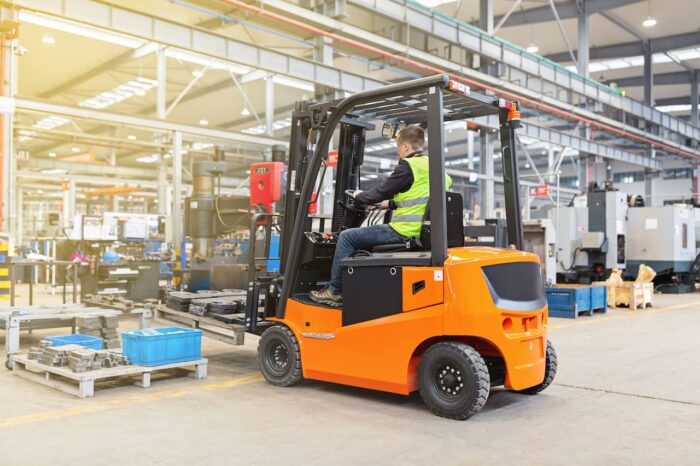
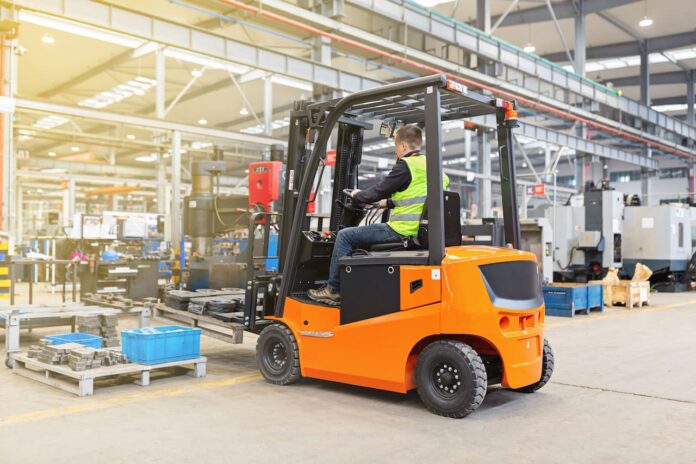
L’efficacité de la gestion des matériaux est essentielle pour optimiser les opérations d’un entrepôt. Une manipulation efficace augmente la productivité et améliore la rentabilité, ce qui en fait une priorité pour tout entrepôt.
1. Fournir aux Employés l’Équipement de Manipulation de Matériaux Approprié
Il est fondamental de garantir que les employés disposent de l’équipement adéquat pour la manipulation des matériaux. Les équipements de stockage et de manutention, tels que les racks à palettes, les racks coulissants, les étagères, les bacs et les mezzanines, permettent une organisation efficace de l’entrepôt.
Les systèmes automatisés comme les AS/RS, les systèmes de livraison robotisés, les convoyeurs et les AGV réduisent le travail manuel et augmentent la rapidité.
Les équipements de manutention en vrac, tels que les bandes transporteuses, les empileurs, les récupérateurs, les élévateurs à godets et les élévateurs à grains, gèrent de grandes quantités de matériaux sans effort.
Pour le transport, les transpalettes, les chariots élévateurs, les stackers manuels, les chariots de plateforme et les AGV facilitent le mouvement des marchandises au sein de l’entrepôt.
Chaque type d’équipement est conçu pour répondre à des besoins spécifiques, améliorant ainsi le flux de travail global et réduisant les risques de goulets d’étranglement.
2. Concevoir un Aménagement Efficace de l’Entrepôt
Un aménagement bien pensé de l’entrepôt est crucial pour des opérations fluides. L’analyse des flux de matériaux et des schémas de circulation aide à définir des zones spécifiques pour le chargement/déchargement, la réception, le stockage, la préparation de commandes et l’expédition.
Organiser les articles en fonction de leur accessibilité et de leur fréquence d’utilisation garantit que les produits à forte demande sont facilement accessibles, minimisant ainsi le temps de récupération.
Des voies dégagées pour les équipements et les employés préviennent la congestion et les accidents, contribuant à un environnement de travail plus sûr et plus efficace.
En plaçant stratégiquement les zones de stockage et d’opération, les entrepôts peuvent maximiser l’utilisation de l’espace et rationaliser les processus, améliorant ainsi la productivité et réduisant les coûts opérationnels.
3. Former le Personnel de l’Entrepôt
Une formation complète du personnel de l’entrepôt est essentielle pour maintenir la sécurité et l’efficacité. La formation à la sécurité pour la manipulation d’équipements lourds protège les employés des blessures et garantit une utilisation appropriée des machines.
Des mises à jour régulières sur les procédures opérationnelles tiennent le personnel informé des meilleures pratiques et protocoles les plus récents. Mettre l’accent sur les techniques de levage appropriées réduit le risque de blessures musculo-squelettiques.
Faire appel à des formateurs qualifiés pour des instructions formelles et des démonstrations pratiques garantit que le personnel est bien préparé à effectuer ses tâches efficacement.
Une éducation continue et le renforcement des mesures de sécurité créent une culture de sensibilisation et de responsabilité, menant à un environnement d’entrepôt plus efficace et sécurisé.
4. Améliorer la Précision des Prévisions
Une prévision précise est essentielle pour gérer efficacement les stocks. La mise en œuvre d’un Système de Gestion d’Entrepôt (WMS) permet un suivi en temps réel des stocks, facilitant un contrôle précis des inventaires.
Anticiper les variations saisonnières de la demande aide à ajuster les niveaux de stock en conséquence, évitant ainsi les surstocks ou les ruptures de stock. Réviser et mettre à jour régulièrement les prévisions garantit qu’elles reflètent les tendances et les demandes actuelles du marché.
Éliminer les articles obsolètes de l’inventaire libère de l’espace précieux et réduit les coûts de stockage.
En améliorant la précision des prévisions, les entrepôts peuvent optimiser leur gestion des stocks, réduire le gaspillage et répondre plus efficacement aux demandes des clients, contribuant ainsi à la rentabilité globale.
5. Assigner des Employés Expérimentés aux Tâches Critiques
Exploiter l’expertise des travailleurs expérimentés pour des tâches critiques garantit des normes élevées d’opération. Les employés chevronnés s’occupant des activités de réception et de stockage assurent précision et efficacité.
Les nouveaux employés peuvent commencer par la préparation de commandes pour se familiariser avec le système d’inventaire et développer une bonne compréhension de l’agencement et des processus de l’entrepôt.
Une approche progressive de l’attribution des tâches maintient non seulement l’efficacité opérationnelle, mais offre également aux nouveaux employés l’opportunité d’apprendre et de se développer dans un environnement structuré.
L’expérience des travailleurs vétérans constitue une ressource précieuse pour maintenir la qualité et la productivité dans des domaines clés.
6. Optimiser les Horaires d’Arrivée des Camions
Optimiser les horaires d’arrivée des camions peut réduire considérablement les temps d’attente et améliorer l’efficacité. En planifiant stratégiquement les livraisons, les entrepôts peuvent minimiser le temps d’inactivité des camions, améliorant ainsi le débit.
Une planification efficace réduit également le besoin d’utilisation extensive des quais, entraînant des économies sur les coûts d’utilité. Coordonner les horaires d’arrivée avec les heures de pointe opérationnelles garantit que les ressources sont disponibles pour gérer les expéditions entrantes rapidement.
Cette approche rationalise non seulement le processus de réception, mais aide également à maintenir un flux de travail constant, prévenant les goulets d’étranglement et maximisant l’utilisation de l’espace et de la main-d’œuvre disponibles.
7. Utiliser des Quarts Séparés pour l’Expédition et la Réception
Mettre en place des quarts séparés pour l’expédition et la réception peut rationaliser les flux de travail et réduire les besoins en zones de staging.
En consacrant des créneaux horaires spécifiques à chaque activité, les entrepôts peuvent s’assurer que les ressources et le personnel se concentrent sur une tâche à la fois, réduisant ainsi la probabilité d’erreurs et de congestion.
La séparation permet également une utilisation plus organisée et efficace de l’espace, car les zones désignées pour l’expédition et la réception ne sont pas occupées simultanément.
Elle permet une meilleure planification de la main-d’œuvre, garantissant que le personnel est alloué efficacement pour gérer les périodes d’activité de pointe pour les opérations d’expédition et de réception.
8. Accélérer les Processus de Déchargement
Accélérer les processus de déchargement est crucial pour réduire la congestion des camions dans la cour et améliorer l’efficacité globale. Évaluer les temps de déchargement par rapport aux normes de l’industrie peut fournir des informations sur les domaines à améliorer.
Mettre en œuvre des meilleures pratiques, telles que l’utilisation d’équipements avancés ou l’optimisation des niveaux de personnel pendant les périodes de pointe, peut réduire considérablement les durées de déchargement.
Minimiser les retards dans le processus de déchargement libère non seulement de l’espace dans la cour, mais accélère également le flux de marchandises dans l’entrepôt, améliorant ainsi le roulement des stocks. Des processus de déchargement efficaces contribuent à des opérations plus fluides et à une meilleure utilisation des ressources.
9. Entretenir les Sols de l’Entrepôt
Un entretien régulier des sols de l’entrepôt est essentiel pour prévenir les dommages aux équipements et aux marchandises, ainsi que pour améliorer la sécurité et la productivité. Des inspections et des réparations de routine peuvent identifier et résoudre les problèmes potentiels avant qu’ils ne s’aggravent.
Des sols bien entretenus réduisent le risque d’accidents causés par des surfaces inégales ou des obstructions.
Ils garantissent également un mouvement fluide des équipements de manutention, prévenant l’usure des machines. Investir dans l’entretien des sols prolonge non seulement la durée de vie des équipements, mais crée également un environnement de travail plus sûr, ce qui est crucial pour maintenir des niveaux de productivité élevés.
10. Améliorer les Opérations d’Emballage
Optimiser les opérations d’emballage est vital pour maintenir un flux de travail cohérent et garantir l’exactitude des commandes.
Les emballeurs doivent disposer de commandes complètes et d’un espace suffisant pour travailler efficacement. Rationaliser le processus d’emballage en organisant les stations d’emballage et en fournissant des fournitures adéquates peut réduire les retards et les erreurs.
Traiter les inefficacités dans le processus de préparation des commandes, telles que les erreurs de sélection ou les pénuries, garantit que les emballeurs ont tout ce dont ils ont besoin pour compléter les commandes rapidement.
Réviser et affiner régulièrement les procédures d’emballage peut conduire à des améliorations significatives en termes de rapidité et d’exactitude, contribuant ainsi à l’efficacité opérationnelle globale et à la satisfaction des clients.
Conclusion
Améliorer l’efficacité de la gestion des matériaux est essentiel pour la productivité et la rentabilité des entrepôts. La mise en œuvre de ces étapes peut entraîner des améliorations opérationnelles significatives, renforçant à la fois la performance et les résultats financiers.
Divertissement
« À la rencontre d’un Hugo : une aventure inattendue »
Le prénom, un véritable reflet de notre identité, peut être à la fois lourd à porter et source de fierté. Dans cette chronique fascinante, le réalisateur Hugo David nous plonge dans son expérience avec un prénom très répandu. Né en 2000, il se retrouve entouré d’autres Hugo, ce qui l’amène à adopter un alias : Hugo D.. Comment ce choix a-t-il influencé son parcours ? Explorez les nuances et les histoires derrière nos prénoms et découvrez comment ils façonnent nos vies dès l’enfance jusqu’à l’âge adulte !
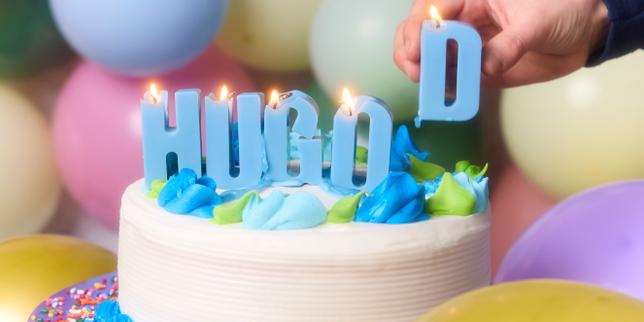
Les Prénoms : Un Voyage au Cœur de l’Identité
Le Rôle Crucial des Prénoms dans nos Existences
Chaque personne possède un prénom, qu’il soit courant ou singulier, et ce dernier peut engendrer à la fois fierté et embarras. Cet article explore la signification profonde et l’influence des prénoms sur notre vie quotidienne. Le réalisateur Hugo David partage son vécu avec un prénom qui a connu une forte popularité durant sa jeunesse.
une Naissance Sous le Signe de la Célébrité
Hugo David est né en 2000 à Tours, une époque où le prénom Hugo était en plein essor. Ses parents, Caroline et Rodolphe, avaient envisagé d’autres choix comme Enzo, également très en vogue à cette période. « Je pense que mes parents ont opté pour un prénom parmi les plus répandus en France plutôt qu’en hommage à Victor Hugo », confie-t-il.
Une Enfance Entourée d’Autres « Hugo »
Dès son plus jeune âge, Hugo se retrouve entouré d’autres enfants portant le même nom. Selon les statistiques de l’Insee,7 694 garçons ont été prénommés Hugo en 2000,faisant de ce prénom le quatrième plus populaire cette année-là. À l’école primaire,il côtoie plusieurs camarades appelés Thibault et autres prénoms similaires. Pour éviter toute confusion lors des appels en classe, les enseignants ajoutent souvent la première lettre du nom de famille après le prénom : ainsi devient-il rapidement « Hugo D. », un surnom auquel il s’habitue sans arduousé.
Pensées sur l’Identité Associée au Prénom
Le choix d’un prénom peut avoir un impact significatif sur notre identité personnelle tout au long de notre existence. Que ce soit pour se distinguer ou pour s’intégrer dans un groupe social spécifique, chaque individu développe une relation particulière avec son propre nom.
les prénoms ne sont pas simplement des désignations ; ils portent avec eux des récits et influencent nos interactions sociales depuis notre enfance jusqu’à l’âge adulte.
Divertissement
M. Night Shyamalan sous le feu des projecteurs : un procès pour plagiat ébranle sa série « Servant » !
Un procès captivant s’est ouvert à Riverside, en Californie, où M. Night Shyamalan fait face à des accusations de plagiat lancées par Francesca Gregorini. Elle affirme que sa série Servant, diffusée sur Apple TV+, est une copie de son film de 2013, The Truth About Emanuel, et réclame la somme colossale de 81 millions de dollars.
L’avocat de Gregorini a présenté des extraits troublants mettant en scène une mère et sa poupée. La défense soutient que le projet était déjà en développement avant la sortie du film. Qui sortira vainqueur ?
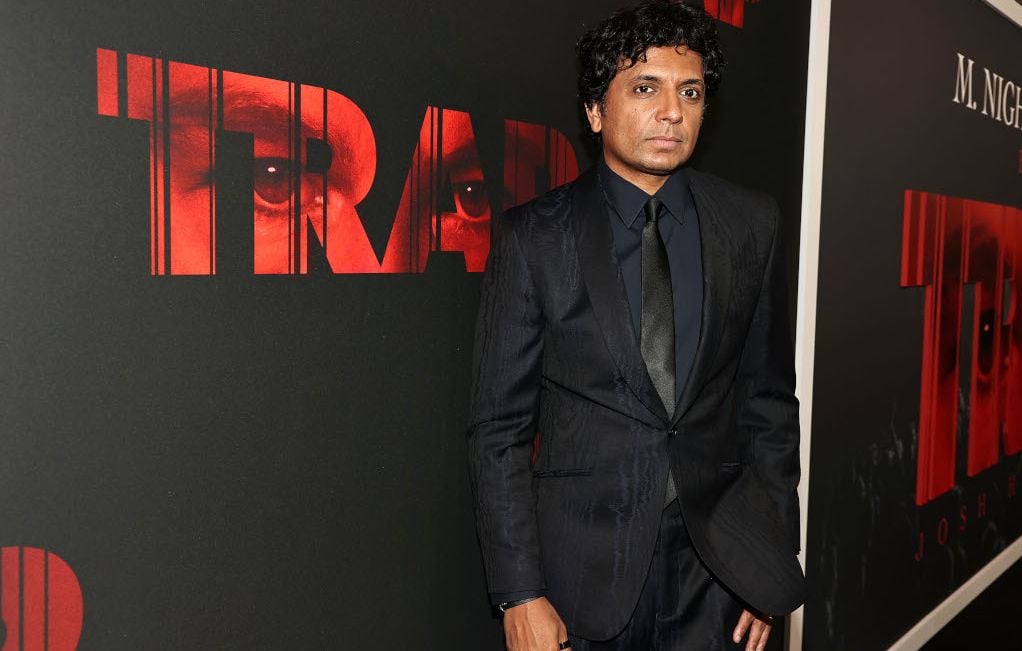
Affaire de Plagiat : M. Night Shyamalan sous le Feu des Projecteurs
Un procès pour plagiat a été lancé ce mardi à Riverside, en Californie, impliquant le réalisateur M. Night Shyamalan. La plaignante, Francesca Gregorini, affirme que la série servant, produite par Shyamalan pour Apple TV+, est une imitation directe de son film The Truth About Emanuel, sorti en 2013. Elle demande des dommages-intérêts s’élevant à 81 millions de dollars.
Accusations Détails et Comparaisons Éclairantes
L’avocat représentant Francesca Gregorini, Patrick Arenz, a présenté au jury des extraits comparatifs entre les deux œuvres. Ces séquences illustrent une mère prenant soin d’une poupée comme si c’était un véritable enfant, assistée par une nourrice. « C’est un cas flagrant », a-t-il déclaré devant le jury selon Variety. »Sans Emanuel, il n’y aurait pas eu de Servant. »
Divergences dans les Arguments Juridiques
En réponse aux allégations portées contre lui, l’équipe juridique défendant Shyamalan soutient que Tony Basgallop, le créateur britannique derrière la série Servant, avait commencé à développer ce projet bien avant la sortie du film de Francesca Gregorini.
« Elle cherche simplement à tirer profit d’un travail qu’elle n’a pas conçu », a affirmé l’avocate Brittany Amadi lors du procès.En 2020, une première plainte avait été rejetée ; néanmoins, la cour d’appel avait rouvert l’affaire en considérant qu’il existait un débat légitime concernant les « similarités substantielles » entre les deux œuvres.Cette affaire soulève des questions cruciales sur l’originalité dans le secteur cinématographique et pourrait avoir des conséquences significatives sur les droits d’auteur et la propriété intellectuelle dans l’univers du divertissement.
Divertissement
Une policière ivre et indisciplinée : une bagarre explosive éclate après un vol de voiture ! Plongez dans les rebondissements de cette affaire incroyable !
Actualité : Une nuit tumultueuse à Agen ! Dans un état d’ivresse, une femme d’une trentaine d’années a mordu une policière lors d’une palpation corporelle. Cette agression inattendue a causé trois jours d’incapacité pour la fonctionnaire, soulignant les dangers auxquels elle fait face au quotidien. La mise en cause, désormais convoquée sur procès-verbal, devra répondre de ses actes impulsifs devant la justice.
Restez avec nous pour découvrir l’évolution de cette affaire et bien plus encore !
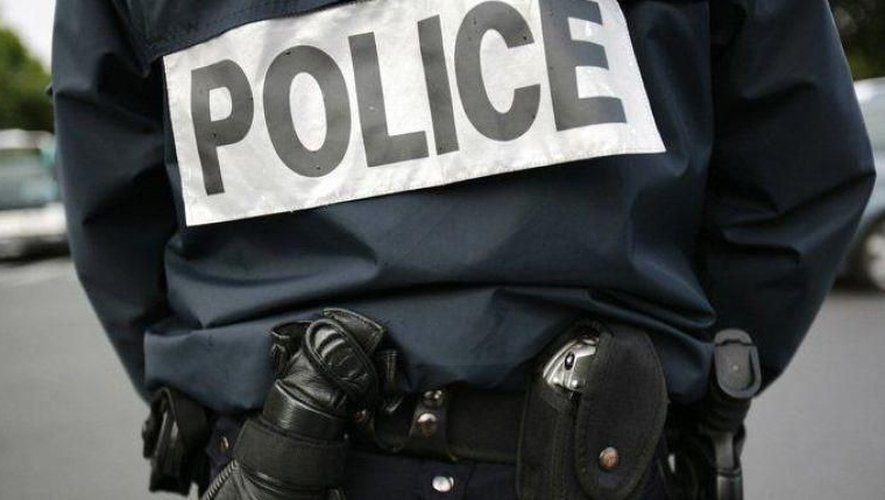
Agression d’une Policière par une Femme en État d’Ébriété
Dans la nuit du 18 janvier, une femme d’une trentaine d’années, sous l’influence de l’alcool, a mordu une agente de police lors d’un contrôle corporel habituel. Cette agression a causé trois jours d’incapacité totale pour la fonctionnaire. En conséquence, l’individu concerné a été convoqué à comparaître suite à un procès-verbal établi.
Renforcement des Sanctions Judiciaires pour les Actes de Violence à Agen
Le 17 janvier aux alentours de 22 heures, une dispute s’est produite sur le boulevard de la Liberté à Agen, impliquant trois hommes. L’un des participants, avec des marques visibles sur son manteau, a déclaré avoir été attaqué au couteau par les deux autres. Ces derniers ont rejeté les accusations lors de leur interrogatoire. Déjà sous le coup d’une obligation de quitter le territoire (OQTF), ils ont reçu une nouvelle OQTF accompagnée d’une assignation à résidence. La victime n’a pas porté plainte et était introuvable à son domicile.
Affrontements et Tentative de Vol : Comparution au Tribunal en Avril
Un autre incident s’est produit à Villeneuve-sur-Lot où plusieurs individus se sont battus après avoir reçu des menaces liées à un vol automobile avorté. Le parquet a décidé de poursuivre trois passagers en leur proposant une comparution sur reconnaissance préalable de culpabilité (CRPC). Ils devront se présenter devant le tribunal local fin avril.
-
Général12 mois ago
X (anciennement Twitter) permet enfin de trier les réponses sur iPhone !
-
Business11 mois ago
Comment lutter efficacement contre le financement du terrorisme au Nigeria : le point de vue du directeur de la NFIU
-
Technologie6 mois ago
TikTok revient en force aux États-Unis, mais pas sur l’App Store !
-
Général6 mois ago
Anker SOLIX dévoile la Solarbank 2 AC : la nouvelle ère du stockage d’énergie ultra-compatible !
-
Sport6 mois ago
Saisissez les opportunités en or ce lundi 20 janvier 2025 !
-
Général6 mois ago
La Gazelle de Val (405) : La Star Incontournable du Quinté d’Aujourd’hui !
-
Science et nature7 mois ago
Des Projets Ambitieux qui Pourraient Redéfinir la Géopolitique
-
Général6 mois ago
Quinté Plus PMU : Rock Boy, un futur champion à surveiller de près !